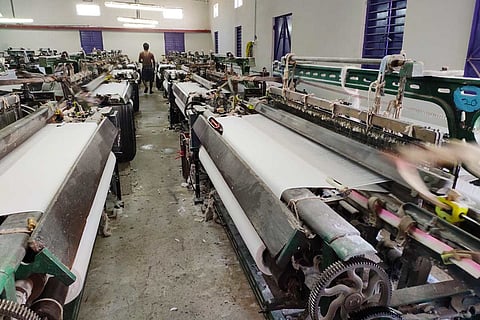
Bronchitis, tuberculosis, weight loss and hearing loss are oft-heard health problems among workers of fine-dust producing industries in the Tirupur-Coimbatore region in Tamil Nadu. With a plethora of cotton spinning mills, garment units and power looms, these fine dust producing industries are the primary employers of rural men and women in the region.
Power loom worker Swamy sometimes requires hospital care due to excessive cough build up. He is unable to take a break to look after his health, although he has been serving the same employer for over 25 years. He also suffers from partial hearing loss, weight loss, and chronic bronchitis. “When I would cough, I would see minute cotton particles in the discharge. With blood in the discharge, I got worried and consulted the doctor. When we go to the government primary health centre (PHC) in the village, they have very specific medicines for power loom workers. So if I have a cough or breathing trouble, they will suggest the same set of medicines every time I go to the PHC,” Swamy said, adding that he also suffered weight loss of over 10 kgs in the last few months.
Nationally representative surveys in India do not capture occupational health diseases. Socio-economic surveys such as the National Sample Survey Organisation primarily collect data on socioeconomic status and employment. On the other hand, health and demographic surveys such as the National Family and Health Surveys capture tobacco and alcohol consumption, high blood glucose, hypertension, obesity, tuberculosis, and reproductive health, but we know little about how this links to the work that people do. Further occupational health nursing is practically absent in the unorganised sectors. There is a paucity of research on health vulnerabilities of garment workers in South and South-East Asia and a recent systematic review shows that workers in these industries are prone to several health vulnerabilities including hearing disabilities, respiratory illnesses, and musculoskeletal discomfort, that need to be better understood and addressed.
Social disadvantage impacts health outcomes, particularly in a deeply stratified caste society as in India. For example, when it comes to knitwear garment industries in Tamil Nadu, the majority of owners are Gounder men of peasant origins, while the workers are landless Dalits and women, particularly since the 1980s. In the absence of caste-wise data on occupational health, we can only observe these differences as they manifest in life expectancy, that is, the number of years a person can expect to live. Evidence from research on the National Family and Health surveys show that individuals from the Scheduled Castes have lower life expectancies than high caste individuals and have persisted over the last two decades. Our qualitative research with 58 respondents in the Tirupur-Coimbatore region shows significant occupational health diseases among informal workers in these industries.
A community-health doctor from the Rural Unit for Health and Social Affairs in Vellore said that the diagnosis depends on whether the patient is genetically predisposed to such complications or if it is because of prolonged exposure to fine dust. He said, “The treatment would differ accordingly. The gold standard diagnosis is a Spirometry test. We ask the patients to get that done and come back with reports. We give them short-acting inhalers which is the gold standard for the treatment. We also give tablets- Deriphyllin and Salbutamol – but they are not solutions but only relievers.”
He said that it was mandatory for all fine dust producing industries to have fixed work hours and regular health check-ups for every employee, but employers bypass these regulations easily. He added, “The loophole in law is that the employee must be a permanent worker. But none of the employers have it on paper that a person is a permanent worker but show that they take people on rotation basis and first-come-first-serve basis. As per law having more than 20 workers demand in-house health checks, but none of them will have 20 workers at a time and sometimes make do with fewer workers and longer working hours.”
The power loom has a high noise level around 94-99 dB, extremely sultry ambience with poor lighting, and flying dust. The doors are almost always kept closed. Work at the power loom is segregated by gender; women are employed in spinning the thread, and men and women work on the looms. Women typically handle six machines or less and men handle up to ten machines.
Older women like Sitamani were among the first generation of workers at the mills and looms that were being set up in Tirupur and Coimbatore districts. Sitamani has diversified from being an agricultural labourer to working in the mills and power looms. The 48-year-old worked at a cotton mill for two years after which she started having breathing problems like wheezing, even as none of her family members have a history of asthma. She said, “Imagine an entire transformer’s heat coming into the mill, it was like that. It would heat up and there would be fine cotton dust flying in the air inside the room full of mill workers.”
Before the national lockdown due to the coronavirus pandemic in 2020, she started working at a banian/vest company. Within a few months, she began showing signs of non-allergic rhinitis for which she blames the air conditioning in the building. However, she continued working at the company. She explained, “The work seems decent as opposed to other jobs I have done.”
Jayamani worked in the packaging section of a garment unit for a brief period of five months in 2019 and ended up with persistent insomnia, weight loss, runny nose, and other health related problems. “People started noticing how my body shrank during that time. People still ask me why I look like this,” she said. The 45-year-old, now works in the handloom industry but said that despite her health problems, she will go back to working in the garment industry if weaving on the handloom becomes unremunerative.
There are few employment options in the region for semi-skilled labourers and high school educated individuals, particularly women. So, when the traditional family occupation such as handloom weaving and agriculture are not feasible, people take to garment industries for their bread and butter or resort to state employment guarantee schemes such as the MNREGA.
Some of the younger workers wear earphones to cut off the noise of the machines in the factory. However, hearing is key because they must attend to a machine that needs a thread refill. Jayan said, “We don’t play anything on our earphones because we have to be attentive when the machine stops working.”
Jayan, who is 29 years old, has been working in the loom for more than half his lifetime. His story is similar to Swamy’s. He said, “Three years ago, when I had gone for my tuberculosis treatment, one of the doctors in the government hospital said that my lungs were 80% damaged and nothing could be done.”
Having to work in an enclosed space, it is common for power loom workers to contract tuberculosis at their workplace and stigma associated with the disease causes additional damage to their families. Jayan said, “I can say from the cough and visible signs like weight-loss that the worker is possibly suffering from TB. They won't say because they would not find any other work and people around them ostracise them.”
Despite repeated complaints by workers, wearing a mask at work is not a choice. Swamy explained, “There would be cotton balls settled in my nasal passage. I have to clean it every now and then and this causes the dust to settle in my eyes. The heat from wearing a mask is unbearable because the ambience of the power loom is already sultry.”
The challenges with wearing masks at work in fine-dust producing industries make workers even more vulnerable to COVID-19. The heat and subsequent sweating make masks less effective as a preventive measure. Lung damage due to tuberculosis further complicates recovery from COVID-19. Runny nose due to non-allergic rhinitis hinders the ability to wear masks. Apart from respiratory and hearing issues, women workers face reproductive health issues such as infertility, stillbirth and irregular menstruation owing to the heat and intensity of work in the garment factories. During the COVID-19 pandemic, non-epidemic health services have taken a backseat, which could potentially impact maternal health of workers in the sector.
Occupational health remains neglected due to the vulnerabilities of the workers as well as unequal power relations with the employers. Studies find a lack of social security measures such as health insurance and provident fund except in a few export-oriented factories. The recent NSS health in India survey 2018 shows that 83% of casual workers in rural non-farm occupations lacked health insurance. Such measures must become the norm in the cotton spinning mills, power looms and garment units in the Tirupur industrial cluster.
Sarayu Srinivasan, R Bhavani, Cibi S and Nithin Deepak are researchers at the French Institute of Pondicherry (IFP). Soundarya Iyer is faculty at RV University and associated researcher at IFP. The authors are grateful to Professor Nitya Rao for her comments. The authors acknowledge the Azim Premji University Research Funding Programme that funds this research.